The Impact of the Pork industry: Main Sources of GHG Emissions from Pork Industry (part 2/4)
Top 5 Insights from "Main Sources of GHG Emissions from Pork Industry"
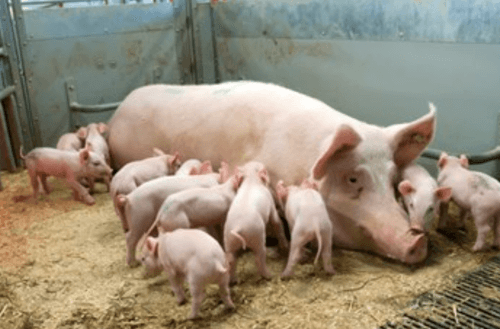
Top 5 Insights from "Main Sources of GHG Emissions from Pork Industry"
- Transportation Emissions: Transporting feed ingredients, processed feed, and pigs significantly contributes to GHG emissions, with feed ingredient transport alone accounting for about 34% of feed production emissions.
- Feed Production Impact: Feed production is a major emission source, mainly from fossil fuel use in cultivation and energy-intensive feed processing, representing 26% to 68% of the pork industry's carbon footprint.
- Energy Use in Pig Production: Intensive pig farming systems consume large amounts of electricity for feeding, ventilation, and heating, contributing 2.6% to 17.0% of the total emissions.
- Methane from Enteric Fermentation: Pigs produce methane through digestion, with strategies like dietary modifications needed to reduce these emissions.
- Manure Management: Methane emissions from manure management are significant, ranging from 19.0% to 56.9% of total emissions, with composting and anaerobic digestion offering mitigation potential.
Transportation
Transportation in this context involves three main stages. Firstly, feed ingredients are transported from their point of origin to feed mills. Secondly, the processed feed is then transported from the feed mills to the farms. Lastly, pigs are transported from the farms to slaughterhouses.
Studies have highlighted that the transportation of feed ingredients is a notable source of GHG emissions within feed production, accounting for approximately 34% of the carbon footprint in this stage. Furthermore, the transportation of animals to slaughterhouses and the subsequent delivery of processed products to markets also significantly contribute to carbon emissions. For instance, research by Chen et al. calculated that the transportation segment in the pork supply chain in China accounts for 52.37% of the GHG emissions across the entire supply chain. The contribution of transportation to carbon emissions can vary widely depending on regional conditions and practices, ranging from 2.2% to 10% of the total emissions in different contexts (Table 1).
Table 1. The contributions of different sources to the GHG emissions of the pork production chain.
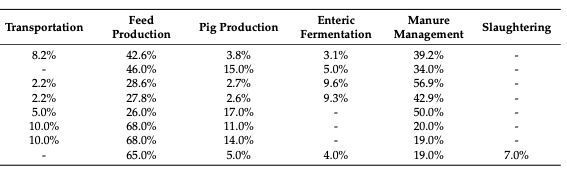
Feed Production
The carbon footprint of feed production in the pork industry is significant, primarily due to the energy consumption involved from the cultivation of crops to the processing of feed. The cultivation of feed crops contributes substantially to carbon emissions, mainly through the use of fossil fuels for seeds, pesticides, fertilisers, and agricultural machinery. According to Zhou et al., the cultivation stage alone accounts for 66% of the total emissions in feed production.
Feed processing also demands considerable energy, which includes electricity for various processes such as material reception, grinding, mixing, conditioning, pelleting, cooling, storage, and packaging. Each of these stages involves specific equipment and machinery that consume electricity, indirectly leading to CO2 emissions. The emission coefficient varies depending on factors such as fuel type, electricity sources, and production efficiency. For example, Fang et al. reported that processing 1000 kg of pig feed generates 28.03 kg of CO2. Given the global production of 322 Tg of pig feed per year, the CO2 emissions from feed processing alone amount to approximately 9.03 Tg annually.
The energy consumption for feed production and processing represents a major portion of the total energy use in pork production, exceeding 50% as noted in some studies. Overall, the contribution of feed production to the carbon footprint in the pork industry ranges from 26% to 68%, highlighting the significant potential for carbon mitigation in this area (Table 1).
Pig Production
The modern pig industry is characterised by intensive and automated production systems, which include automatic feeding management and environmental control. These systems involve feed transport, automatic feeding, ventilation, insulation, and heating in pig houses, all of which consume substantial amounts of electricity. Additionally, lighting systems, especially the provision of 16 hours of lighting for sows to promote oestrus, contribute to energy consumption. Although the electricity used for lighting is relatively low compared to the total electricity consumption, it is still a noteworthy factor when calculating the carbon emissions of the entire pig production chain. Paris et al. highlighted that 50% of the energy required to produce 1 kg of pork is related to electricity consumption on pig farms.
Pig production also involves various consumables, such as medications, cleaning supplies, personal protective equipment, maintenance items, vaccinations, and semen collection supplies. The production and transportation of medications, which include vaccines, immune enhancers, and treatment drugs, consume energy and contribute to GHG emissions. Maintaining cleanliness and hygiene in pig pens requires disinfectants and detergents, whose production and transportation also lead to carbon emissions. The maintenance of pens and electrical equipment further adds to energy use and carbon footprints, which can vary significantly depending on regional differences, environmental conditions, and management practices. According to available data, the contribution of the pig production sector to emissions ranges from 2.6% to 17.0% (Table 1).
Enteric Fermentation
Enteric fermentation is a natural digestive process in pigs and other livestock that contributes significantly to GHG emissions, particularly CH4. This process involves the breakdown of organic matter in the digestive system by microorganisms, producing gases such as CH4, CO2, and H2 as by-products.
In pigs, methane-producing bacteria in the intestines convert CO2 and H2 into CH4. This methane production is closely related to the animal’s growth stages and the dietary fibre content of their feed. As pigs grow and their diet changes, the amount of methane they produce can vary significantly. For example, growing pigs on a standard diet can emit between 0.2% to 0.5% of their gross energy intake as methane, translating to approximately 3.4 litres of methane per day for an average slaughter pig. Globally, the contribution of CH4 emissions from enteric fermentation in pigs is substantial. Although it is generally lower compared to ruminants like cattle, it still plays a crucial role in the overall carbon footprint of pig production. In the United States, for instance, enteric fermentation from swine contributes to around 21 million metric tonnes (MMT) of CO2 equivalent emissions annually, which includes emissions from manure management.
Addressing methane emissions from enteric fermentation in pigs involves various strategies, such as dietary modifications to reduce fibre content and enhance feed efficiency, which can help lower methane production. These strategies are crucial for mitigating the environmental impact of pig production and achieving more sustainable livestock farming practices.
Manure Management
The management of pig manure significantly contributes to GHG emissions, primarily CH4. The process starts with microbial activities that decompose organic matter into volatile fatty acids, CO2, and H2. This microbial activity generates heat, creating an optimal environment for methanogenic bacteria to convert acetate, CO2, and H2 into methane under thermophilic conditions.
Studies have shown that carbon emissions from pig manure during composting are particularly high compared to other livestock and poultry manure. Factors such as the materials used for composting, the initial carbon-to-nitrogen ratio (C/N), moisture content, and ventilation rate all influence GHG emissions from manure management. For example, it is estimated that pig manure management can produce around 18 g/CH4/day per pig using machine learning algorithms to model emissions accurately. Manure management practices, such as anaerobic digestion, can significantly mitigate methane emissions. In the United States, various anaerobic digestion systems are employed, with covered lagoons being the most popular, processing manure from nearly 400,000 hogs at over 20 sites. These systems help capture CH4, which can then be flared or used to generate renewable energy, reducing overall emissions. However, economic barriers remain, as implementing anaerobic digestion systems often requires significant capital investment and changes to existing manure management practices. Lastly, the contribution of manure management to the overall GHG emissions of the pork production chain varies widely, ranging from 19.0% to 56.9% (Table 1), depending on the specific management practices and regional conditions.
Wastewater
The wastewater management process in pig production involves several steps, each with specific machinery and energy consumption requirements that contribute to GHG emissions.
First Step: Filtration via Grid System
The initial step in wastewater management involves a grid system that removes solids and floating particles from the wastewater. This step primarily consumes energy through the machinery used for filtration. The efficiency of this process is critical to reducing the load on subsequent treatment stages.
Second Step: Collection System
In the second step, a collection system balances the wastewater and adjusts its volume. The main energy consumption in this step comes from mixers that homogenise the wastewater, ensuring consistent treatment in the following stages.
Third Step: Solid-Liquid Separation System
This stage involves separating solid faeces from the liquid component through filtration and screw pressing. The solid-liquid separator is the primary energy consumer here, as it performs the mechanical separation needed to reduce the volume of solids in the wastewater. The anaerobic system process employs anaerobic bacteria to ferment dissolved organic carbon (DOC) in the wastewater. During this process, DOC is hydrolysed, producing CH4 and removing organic matter from the wastewater. This stage is crucial for reducing the organic load and generating biogas, which can be captured and utilised as an energy source.
Final Step: Further degradation
The final treatment stage involves aerobic processes to further degrade organic pollutants and provide denitrification and phosphorus removal, thereby improving the quality of the effluent to meet discharge standards. This stage consumes significant electricity, particularly through the use of water pumps, circulation pumps, and blowers that ensure adequate oxygenation and mixing.
Slaughtering
The carbon footprint of the pig slaughtering process, although often less discussed, is a significant contributor to overall GHG emissions in pig production (Table 1). Studies have shown that the carbon footprint of pig production varies from 0.6 to 6.75 kg CO2e per kg of pig live weight. Slaughtering and processing require substantial energy for refrigeration, ventilation, heating, and equipment operation, which all contribute to carbon emissions. Additionally, these operations use large amounts of water for cleaning, sanitation, and processing, further adding to the carbon footprint through energy consumption for water heating and wastewater treatment.
Refrigeration and cold storage, essential for maintaining meat quality, consume significant amounts of electricity, leading to additional CO2 emissions. In China, for instance, it was reported that slaughtering and processing pork consume approximately 81.2 kWh of energy and produce 22.08 kg of CH4 emissions per 1000 kg of carcass weight. This underscores the importance of employing energy-efficient technologies and low-energy refrigerants to reduce emissions.
The carbon footprint associated with slaughterhouse operations and meat processing can vary widely depending on the energy sources, waste management practices, and processing techniques employed. According to Wei et al., the carbon footprint of pork is about 3.8 kg CO2e per kg, with slaughtering contributing approximately 7% to the overall emissions of the pork production chain. Different pork products also have varying environmental impacts, with one serving of pork cuts (1 kg) equating to 2.25 to 4.52 kg CO2e.
Action Steps for Reducing GHG Emissions in the Pork Industry
- Improve Transportation Efficiency: Optimise logistics and make the switch to EV to reduce emissions from transporting feed and pigs.
- Enhance Feed Production: Source sustainable feed ingredients and invest in energy-efficient processing technologies.
- Adopt Better Manure Management: Implement anaerobic digestion or composting to reduce methane emissions from manure.