The impact of the pork industry: Case Studies on Reducing Environmental Impacts in the Pork Industry (4/4)
In this blog post, we explore two case studies demonstrating significant advancements in reducing environmental impacts in the pig production industry.
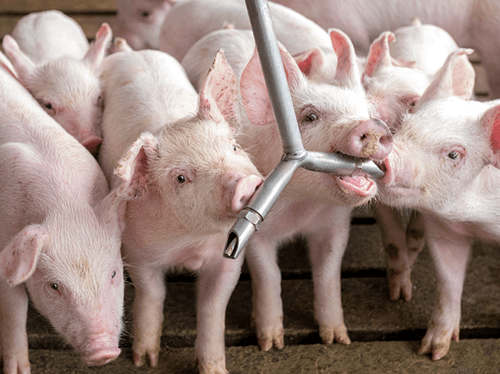
Case Studies on reducing environmental impacts in the pork industry (4/4)
Introduction:
In this last blog post of the pork industry, we explore two case studies demonstrating significant advancements in reducing environmental impacts in the pig production industry. The first case study delves into the 18-year transformation of pig production in the UK, highlighting reductions in environmental impacts through innovative Life Cycle Assessment (LCA) techniques. The second case study examines a revolutionary process for converting pig manure into biochar, offering a sustainable solution for waste management and greenhouse gas reduction.
What You Will Learn:
- How the UK pig production industry has reduced its environmental footprint over the past 18 years.
- The impact of changes in feed composition on environmental metrics.
- The innovative Manure To Biochar (MTB) process and its environmental benefits.
- Key findings and statistical improvements in reducing greenhouse gases, air pollution, and energy consumption.
Key Takeaways:
- UK Pig Production Transformation:
- Significant reductions in environmental impacts such as GWP (37% indoors, 35% outdoors), TAP, FEP, ALU, and FRS.
- Effective use of LCA methodology to track and quantify changes.
- Shift towards more sustainable feed compositions, reducing energy requirements and emissions.
- Manure To Biochar Process:
- Introduction of an efficient process converting manure to biochar, drastically cutting down greenhouse gas emissions and ammonia pollution.
- The MTB process is energy-efficient, reducing consumption to less than one-tenth of traditional methods.
- Successful pilot demonstrations and commercial viability, with plans for scaling up to meet international demand.
By examining these case studies, you will gain insights into innovative methods and technologies that can significantly mitigate environmental impacts in the pig industry.
Case Study 1: Tracking back the last 18 years of pig production in the UK
Over the past two decades, the pig production industry in Great Britain has undergone significant transformations, aimed at reducing its environmental impacts. The study “Changes in the environmental impacts of pig production systems in Great Britain over the last 18 years” by Ottosen et al. (2021) provides a comprehensive analysis of these changes through a novel LCA approach. The LCA method developed in this study addresses the challenges posed by sparse historical data, enabling an accurate estimation of environmental impacts resulting from pig production over a span of 18 years.
To quantify these changes, the study integrates nutritional requirement modelling and feed composition analysis into the LCA framework, using historical data from the Agricultural and Horticultural Development Board (AHDB). The findings reveal substantial reductions in environmental impacts across various categories for both indoor and outdoor pig production systems. For instance, global warming potential (GWP) decreased by approximately 37% for indoor systems and 35% for outdoor systems. Similarly, significant reductions were observed in terrestrial acidification potential (TAP), freshwater eutrophication potential (FEP), agricultural land use (ALU), and fossil resource scarcity (FRS).
Changes in feeding composition
The changes in feed composition for indoor and outdoor bred pigs over the last 18 years are illustrated in Figure 3. For both indoor and outdoor bred pigs, there was a significant shift in the types of feed ingredients used. Notably, the use of wheat and oils decreased, while the inclusion of barley and various co-products increased. These changes were driven by a general reduction in the energy concentration required in the feed for finisher pigs and gilts. Specifically, the energy concentration for finisher feed dropped from 13.7 to 11.0 MJ ME/kg over the period, reflecting an adjustment to typical feed specifications.
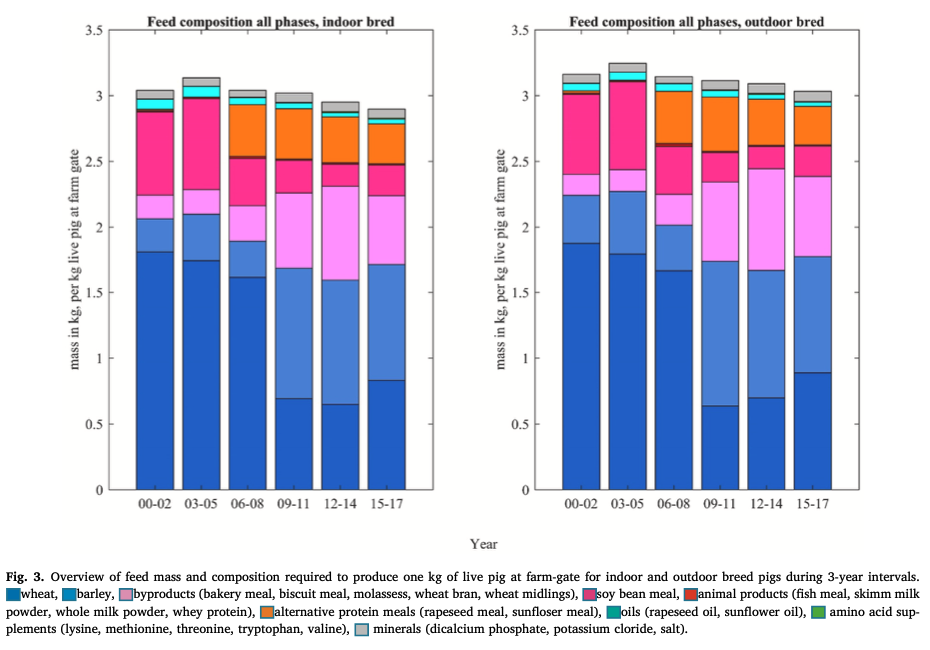
The inclusion of soybean meal in the feed also decreased, supplemented instead by an increased use of pure amino acid supplements. However, the levels of tryptophan and valine remained unchanged. Despite these variations, the protein concentration in feeds for production pigs remained relatively stable throughout the period. The trend towards greater use of amino acid supplements can be attributed to their reduced costs, making them a more economically viable option for maintaining the necessary nutritional balance in pig feed.
Environmental Impacts on based on the different feeding composition
The trends in the predicted relative environmental impacts for indoor and outdoor bred pigs from 2000 to 2017 are illustrated in Figure 4. Following an initial increase during 2003–2005, all environmental impacts exhibited a downward trend, stabilising towards a plateau by 2015–2017.
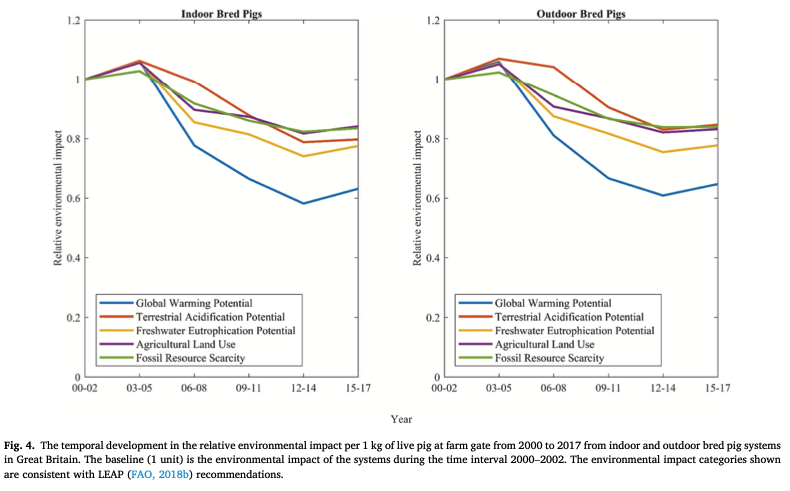
Over the period from 2000 to 2017, the GWP per kilogram of live weight for indoor bred pigs decreased by 37.0%, from 3.82 to 2.41 kg CO2 equivalent per kilogram of live weight. Moreover, TAP, FEP, ALU, and FRS were reduced by 21.2, 22.55, 15.8, and 16.5% respectively. Similarly, for outdoor bred pigs, GWP per kilogram of live weight decreased by 35.4%, from 3.82 to 2.47 kg CO2 equivalent per kilogram of live weight. TAP, FEP, ALU, and FRS were reduced by 16.4, 22.3, 16.8, and 16.1%.
The early weaner phase made minimal contributions to the overall environmental impacts, accounting for 5.35%, 3.66%, 5.68%, 3.13%, and 5.70% for GWP, TAP, FEP, ALU, and FRS, respectively, due to the small feed intake during this phase. The finishing phase had the highest contribution to all environmental impacts, with average contributions of 31.6%, 39.3%, 36.5%, 40.5%, and 38.7% for indoor bred pigs, and 31.0%, 44.7%, 35.6%, 39.4%, and 37.9% for outdoor bred pigs for GWP, TAP, FEP, ALU, and FRS, respectively.
The finishing phase was also a significant factor in the reduction of GWP, contributing 41.4% less in 2015–2017 compared to 2000–2002. The reproduction phase was associated with large reductions in GWP, TAP, FEP, ALU, and FRS, with reductions of 55.9%, 39.1%, 46.7%, 41.4%, and 37.9% for indoor bred pigs, and 49.3%, 32.6%, 44.3%, 41.9%, and 34.8% for outdoor bred pigs between 2000 and 2017.
Case Study 2: Converting manure to Black Gold, “Biochar” (Biomass + Charcoal)
Traditional methods of manure management, such as composting and liquid fertilisation, contribute to greenhouse gas emissions and air pollution. However, a new technology developed by Dr. Ji-ho Yoo and his research team from the Korea Institute of Energy Research (KIER) offers a promising solution. This case study evaluates the environmental impacts of converting pig manure into biochar using the newly developed Manure To Biochar (MTB) process.
As of 2022, South Korea produced approximately 50 million tonnes of livestock manure annually, with 87% being used as compost or liquid fertiliser after long-term fermentation. This process, lasting over 60 days, emits significant amounts of N2O and NH3, which contribute to greenhouse gas emissions and air pollution, respectively. The MTB process developed by KIER addresses these issues by rapidly converting livestock manure into biochar within a day, significantly reducing the environmental footprint.
The MTB Process
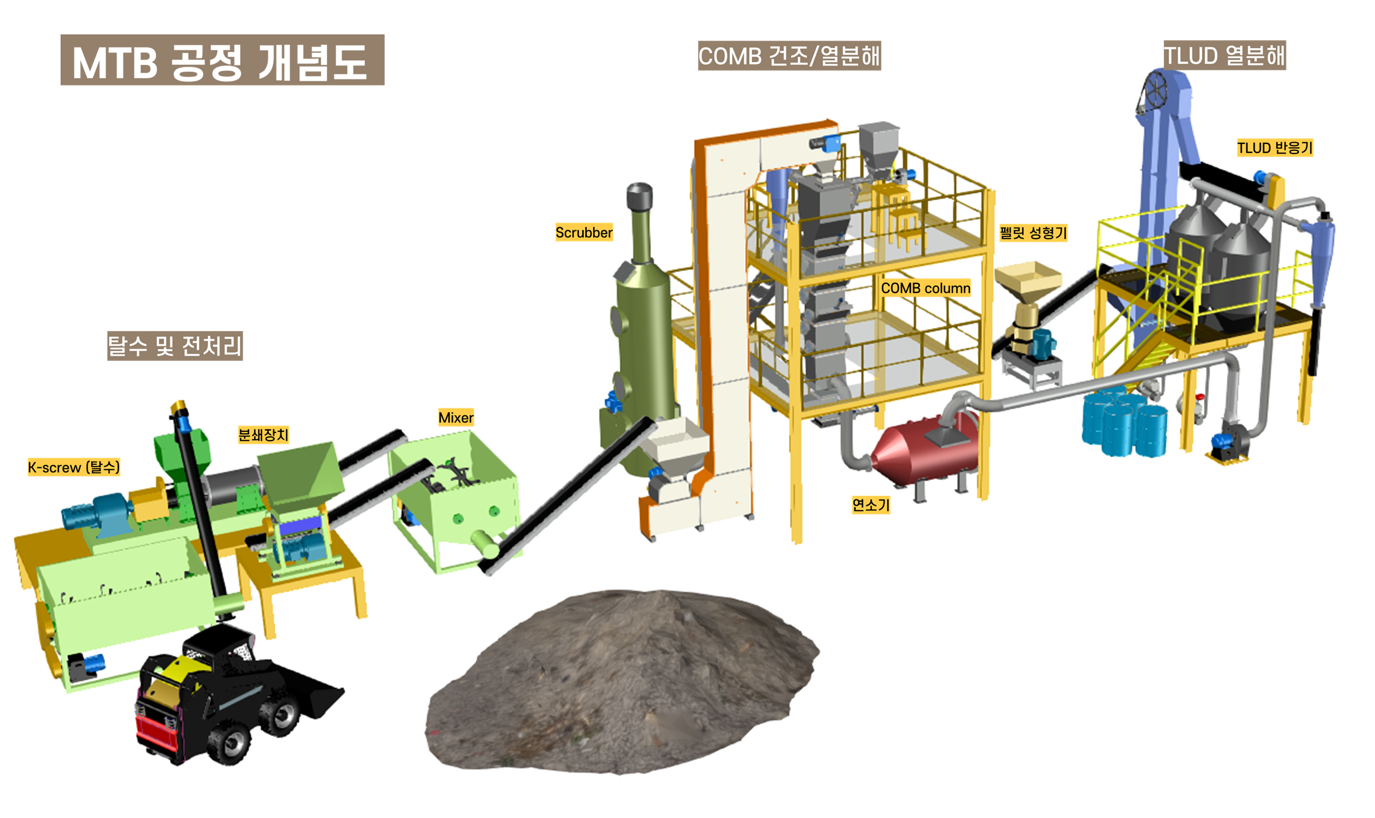
Figure 1. Conceptual diagram of the integrated MTB process
1. Dehydration: Using a screw-type solid-liquid separator developed by the Korea Institute of Machinery and Materials (KIMM), the moisture content in pig manure is reduced from over 80% to less than 60%. This step uses only 1% of the energy required by conventional heat-based processes such as the rotary kiln method.
2. Crushing: The dehydrated manure is finely crushed to less than 1 cm using a three-stage blade crusher developed by DULI TECH Co., Ltd.
3. Drying: The F-COMB drying device developed by KIER further reduces the moisture content to less than 20% in just one minute. This device is designed to maximise heat exposure by allowing manure to fall in a zigzag pattern with hot air from below.
4. Pyrolysis: The dried manure is then converted into biochar using a TLUD (Top Lit Up-Draft) pyrolysis reactor commercialised by YOUGI IND Co., Ltd. This reactor operates at temperatures of 350°C, ensuring efficient conversion to biochar.
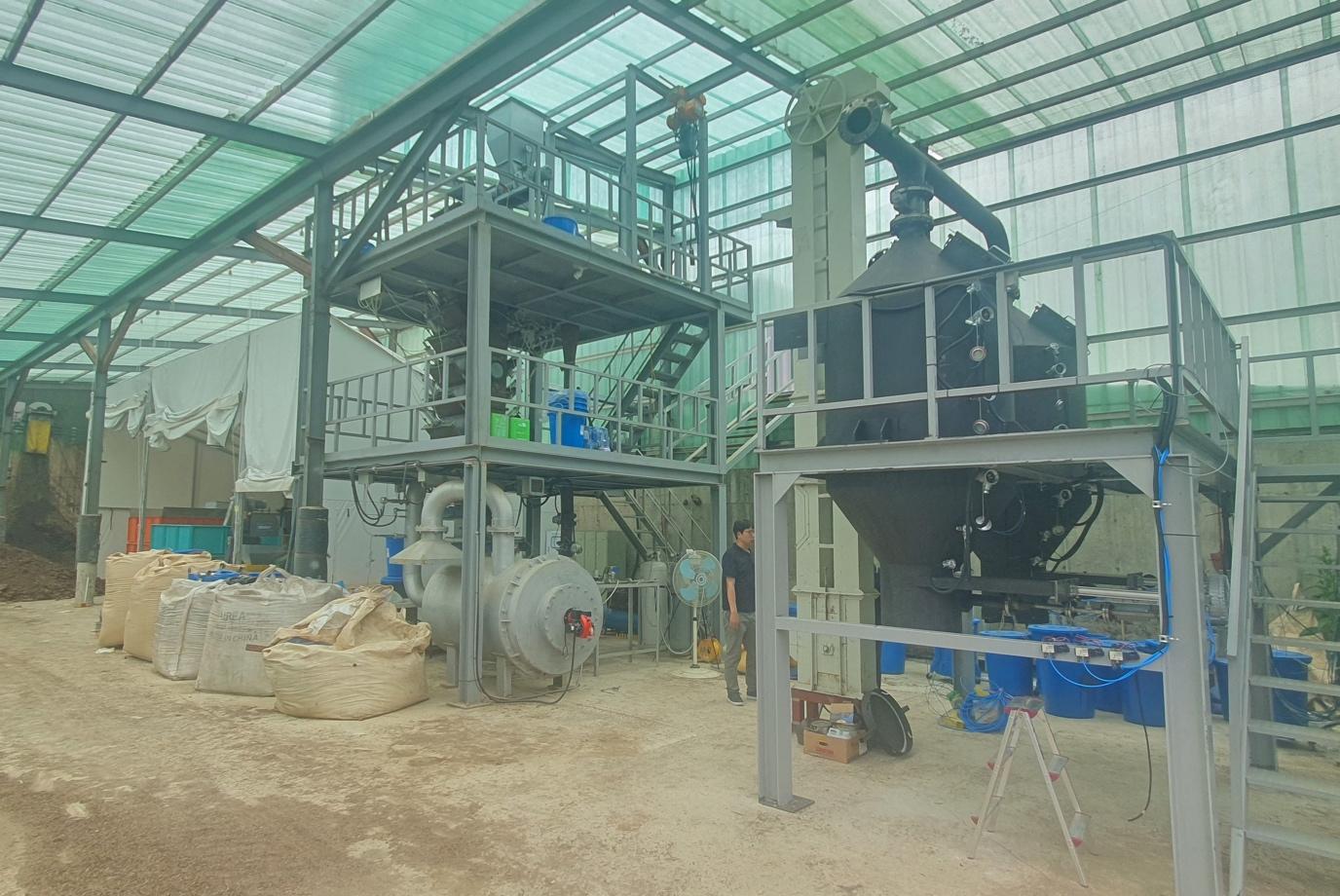
Figure 2. Overview of the MTB setup at the demonstration site in South Korea
Environmental Impact Reduction via the MTB
The MTB process demonstrates significant reductions in environmental impacts compared to traditional manure management methods:
1. Greenhouse Gas Emissions: The conversion of pig manure into biochar prevents the emission of nitrous oxide, a greenhouse gas 300 times more potent than carbon dioxide. Additionally, the biochar sequesters carbon, contributing to carbon neutrality in the livestock sector.
2. Air Pollution: The process eliminates ammonia emissions, which are a major source of ultrafine dust and odours, accounting for 70% of the total ammonia emissions nationwide.
3. Energy Efficiency: The integrated system designed by KIER reduces overall energy consumption to less than one-tenth of that required by conventional rotary kiln methods.
Demonstration and Commercial Viability
The MTB process has been successfully demonstrated at a pilot site in Cheongyang County, Chungnam, with a capacity to handle 10 tonnes of livestock manure per day. The research team completed 100 hours of operation, proving the commercial viability of the technology. The F-COMB drying device developed by KIER is highly competitive in terms of energy efficiency, production cost, and convenience.
Plans are underway to scale up the process to handle more than 100 tonnes per day to meet domestic and international demand, including markets in China, Australia, and Indonesia, who are pushing for environmentally friendly waste management and recycling.
Want to learn more and get a demo? Unibloom empowers sustainability teams to collaborate with cross-functional operations and suppliers in one platform, with data-driven and digital robust Lifecycle Analysis data, to identify the most cost-efficient reduction and investments of your agricultural emissions and make right trade-offs towards Science-Based Targets in minutes, not years. Book: calendly.com/anna-sandgren